When it comes to welding, the distance between the electrode’s end and the base metal’s surface plays a crucial role in achieving optimal results. This parameter, known as arc length, can greatly impact the quality and integrity of the weld joint. In this article, I’ll delve into the significance of maintaining an appropriate distance and how it affects various aspects of the welding process.
Distance Between the End of the Electrode and the Surface of the Base Metal
The Impact of Electrode Length
When it comes to welding, the distance between the electrode’s end and the base metal’s surface plays a crucial role in ensuring a successful weld. One important factor to consider is the length of the electrode itself. If the electrode is too short, it can lead to insufficient heat transfer and penetration, resulting in weak welds that are prone to failure.
On the other hand, if the electrode is too long, it can cause excessive heat buildup and spatter, leading to an inconsistent weld bead.
To illustrate this point further, let’s look at an example. Imagine you’re working on a project requiring welding two thick steel pieces together. If you use an electrode that is too short for this task, you may struggle to penetrate both pieces adequately. As a result, your weld may lack strength and integrity.
Effects of Current Intensity on Distance
Current intensity or amperage is another aspect to consider when maintaining the correct distance between the electrode and base metal. The current intensity determines how much heat will be generated during welding. By adjusting this parameter and maintaining a suitable distance from the workpiece, you can control factors such as penetration depth and weld profile.
If you increase the current intensity without adjusting your distance accordingly, there’s a risk of excessive heat input into the base metal. This can lead to burn-through or even melting through thinner materials like sheet metals.
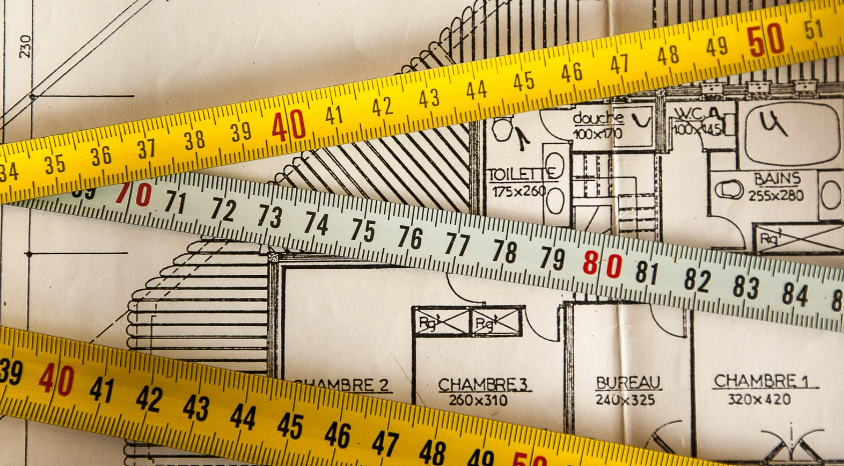
Methods for Measuring the Distance
Standard Methods for Distance Measurement
Several standard methods can be employed when measuring the distance between the end of the electrode and the surface of the base metal. These methods have been widely used in various industries and provide reliable results. Here are a few common techniques:
- Caliper Measurement: One of the most straightforward methods is using a caliper to measure the distance directly. This involves manually positioning the caliper’s jaws on either side of the gap and reading of the measurement displayed on its scale.
- Depth Gauges: Another commonly used method is utilizing depth gauges, specialized tools designed specifically for measuring distances within confined spaces or gaps. These gauges typically consist of a probe that can be inserted into narrow openings, allowing accurate measurements to be obtained.
- Optical Microscopes: Optical microscopes equipped with calibrated reticles or digital measurement systems can also be employed for distance measurement. By focusing on both ends of the gap and aligning specific points under magnification, precise measurements can be obtained by analyzing discrepancies in position.
Alternative Techniques for Measuring Distance
While standard methods provide accurate results, alternative techniques have emerged that offer additional benefits in certain situations:
- Ultrasonic Testing: Ultrasonic testing involves emitting high-frequency sound waves into a material and analyzing their reflections to determine distance measurements accurately. This technique is particularly useful when dealing with non-metallic materials or complex geometries where direct contact-based measurements may not be feasible.
- Laser Scanning: Laser scanning technology has gained popularity due to its ability to capture detailed 3D representations of surfaces quickly and accurately. By scanning both ends of the gap using laser beams, distance measurements can be derived from point cloud data generated by these scanners.
- Proximity Sensors: Proximity sensors utilize electromagnetic fields or infrared light to detect gaps or distances between objects. These sensors can provide real-time distance measurements without physical contact, making them suitable for dynamic environments or limited direct access.
Maintaining the correct distance between the electrode’s end and the base metal’s surface is vital for achieving high-quality welds. The impact of electrode length, the effects of current intensity on distance, and the influence of base metal thickness all contribute significantly to weld integrity and strength.
Considering these factors will help ensure successful welding projects while minimizing potential issues such as weak welds, distortion, or inadequate penetration.